>> Japanese |
 |  |
■ ContactޥޥޥProduction GM Hirohiko Nakahama
■ PhoneޥޥޥޥޥPhone.+81-86-456-3877 FAX.+81-86-455-1591 E-Mail: info@kbknet.co.jp |
Kurashiki Boring Kiko (KBK) is certified ISO9001:2000 in 2005. Careful operation control at each process is essential for assuring the coating performance after thermal spraying, therefore, we utilize our control system to provide our customers with excellent products. |
【Technology and Product】
We are the company which is capable of meeting customer needs which upgrade day-by-day as we employ integrated production system from development, designing, surface modification (thermal spraying), machining, and to finishing. We wish to supply 10~50 pieces of products per month as one lot. We can solve your surface treatment problems quickly. Please feel free to contact us at anytime.
Next generation wear-resistant and corrosion-resistant coating
The thermal spraying, is certified as an alternative surface treatment technology, which replaces chrome plating, by the aircraft manufacturers such as Boeing and Airbus. In the past, chrome was plated onto the parts such as landing gears, but now the thermal spraying is adopted. Currently in many cases, the thermal spraying is utilized as it is environment-friendly and high quality.
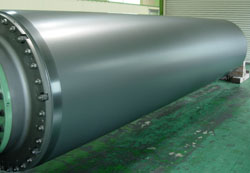
■ Advantages
・Automatic HVOF thermal spraying enables to form dense coating with high adherence performance efficiently. (Please see the moving image)
・Wear-resistant, corrosion-resistant, fatigue-resistant which have advantages over hard chrome plating.
■ Range of application
Landing gear, Turbine, Shaft, Fan blade, and others
■ Processing accuracy
Coating thickness : 80~120μm
■ Material availability
It is possible to apply various different substrate such as titanium, aluminum alloy, and plastics.
Thermal barrier coating (thermal barrier coating, hot corrosion resistive coating)
For aircraft engine components, countermeasures to heat are extremely important. KBK provides our customers with excellent thermal barrier coating which meets every specification of engine manufacturers.
■ Advantages
Plasma spraying forms coating of high melting point materials, such as ceramics and cermet.
■ Range of application
Combustion chambers, turbine blades, and others
■ Processing accuracy
Coating thickness : 0.5~0.7μm
■ Material availability
It is possible to apply various different substrate such as titanium, aluminum alloy, and plastics.
【Company Profile】
■ Company Name | : |
Kurashiki Boring Kiko Co., Ltd. (KBK) |
■ Representative | : |
President Toshiro Tajiri |
■ Address | : |
〒712-8052 2-4-20 Matsue, Kurashiki, Okayama, Japan |
■ Establishment | : |
1957 |
■ Capital | : |
30 million yen |
■ Employees | : |
82 |
■ Major products | : |
Thermal spraying, precise machining, rotary machines |
■ Remarks | : |
ISO certification:
ISO9001 certified: Headquarter and Kamogata factory
[Contemporary Master Craftsman] award winner (2008)
[Genkina Monozukuri SMEs 300] nomination(2008)(METI)
[3rd Monozukuri Japan Award 1st Prize] winner (2009)
Qualified as high pressure gas handling entity |
■ Web site URL | : |
http://www.kbknet.co.jp/english/ |